100N 200N 500N 1000N 2000N 1Nm 2Nm 5Nm 10Nm 20Nm Six axis load cell 6 axes force torque sensor
Model:YGX74 6 axis load cell
Features & Applications:
1. Three dimensional force, three torque and three inclination digital sensor.
2. Software decoupling and inter dimensional coupling error is less than 1%.
3. The sensor has been accurately tested and decoupled before delivery.
4. Supporting handheld instrument or upper computer debugging software.
5. Provide multiple application cases to assist customers in application research.
6. Multiple communication interfaces, convenient for communication and connection with various upper computer equipment.
7. Bending resistant cable with long service life.
Capacity: Fx/Fy/Fz:100/200/500/1000/2000N Mx/My/Mz:1/2/5/10/20Nm(Custom-made is available)
Fx
|
Fy
|
Fz
|
Mx
|
My
|
Mz
|
Weight
|
Flange size
|
100N
|
100N
|
200N
|
1Nm
|
1Nm
|
2Nm
|
1.2kg
|
Φ86
|
200N
|
200N
|
500N
|
2Nm
|
2Nm
|
5Nm
|
1.2kg
|
Φ86
|
500N
|
500N
|
1000N
|
5Nm
|
5Nm
|
10Nm
|
1.2kg
|
Φ86
|
1000N
|
1000N
|
2000N
|
10Nm
|
10Nm
|
20Nm
|
1.2kg
|
Φ86
|
Specifications:
Weight
|
About1.2kg
|
Size
|
Φ86mm×42mm
|
Overload
|
500%FS
|
Accuracy class
|
Accuracy
|
1% FS
|
Nonlinear
|
<0.2% FS
|
Hysteresis
|
<0.2% FS
|
Repeatability
|
<0.2% FS
|
Creep
|
<0.2% FS(30 min)
|
Temp effect on zero
|
0.1%FS/℃
|
Crosstalk
|
<1% FS
|
Natural frequency
|
Natural frequency
|
5000Hz
|
Rigidity
|
500-600 N/μm
|
Inclination measurement
|
Dip angle scale
|
0.1°
|
Dip angle accuracy
|
0.8°
|
Interface characteristics
|
Communication interface
|
RS485
|
Data update rate
|
40Hz
|
Communicating protocol
|
Modbus-RTU
DST-ASC
|
Working environment
|
Power
|
10-30V DC <50mA
|
Operating temp range
|
-10~70℃
|
Dimension(mm):
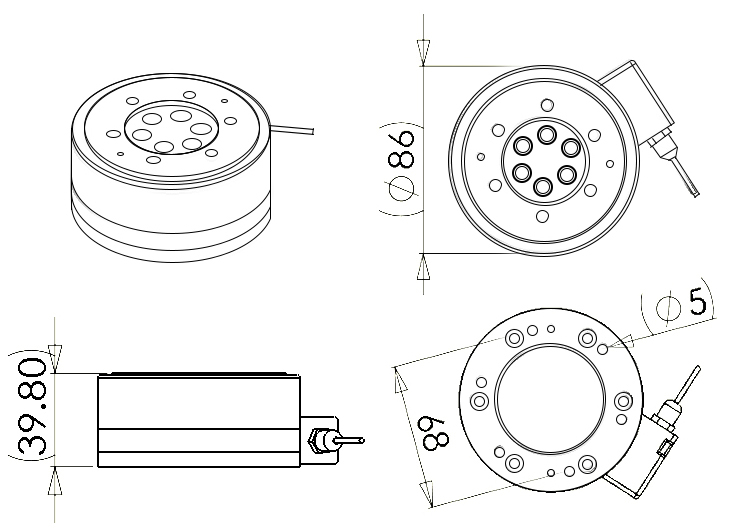
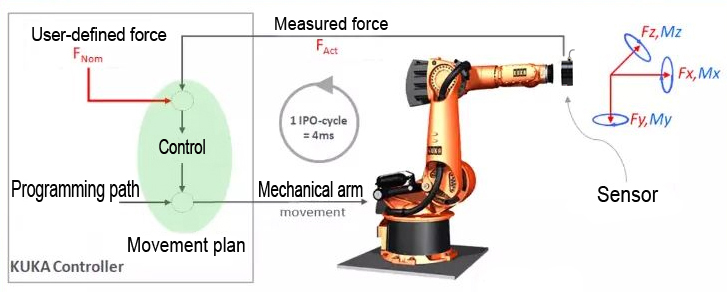
Loading
Force measurement
YGX74 sensor has four common specifications and models, ranging from 100N to 1000N, allowing overload 500%. When the total load at the front end of the sensor is large, or the acceleration height is large when the machine arm is running, the impact of the total load inertia on the sensor should be considered, so the sensor range should be reserved sufficiently balance.
The range of the sensor in all directions is different.
As the need is slightly larger or slightly smaller than the XY axis. After the internal software is decoupled, the dimension coupling error ensures that it is less than 1%.
The sensor is marked with the direction of XYZ axis. When using, pay attention to the influence of the angle deviation versus the measured value. The upper and lower flanges have locating pins to ensure the installation accuracy.
In addition, the XY axis force application point is not the center point of the sensor, that is, if the force arm is not 0, when the force is applied, additional force arms will be generated
Applications
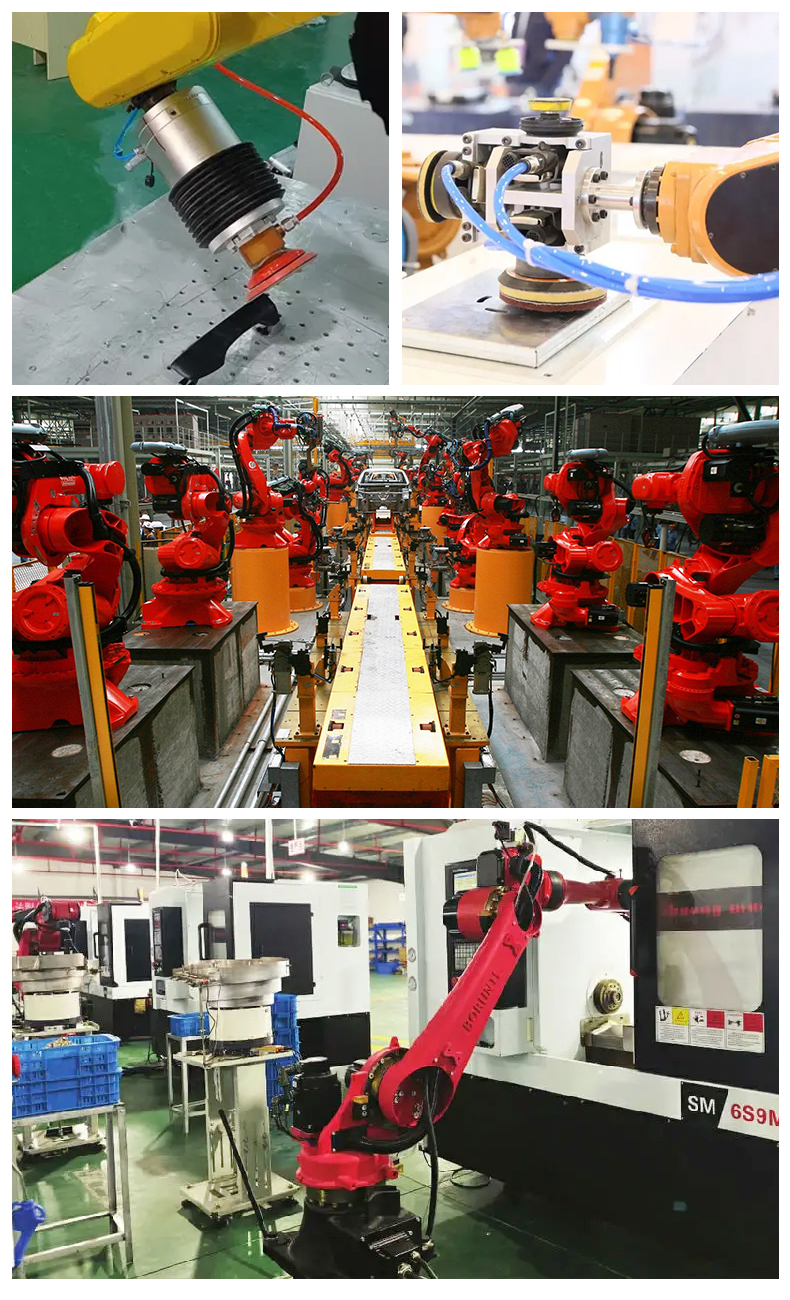